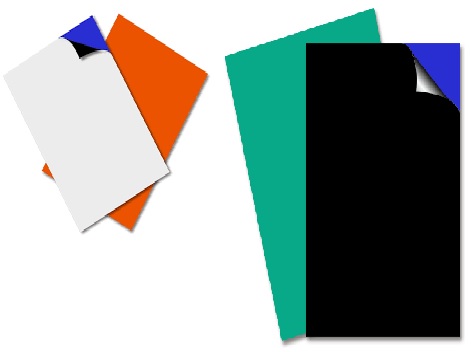
Zinc Etching Plates
Our etching system provides A Grade Zinc Plates which are pre-sanitized and mom sensitized polished plates.
The Zinc plate starts with highest grade zinc spelter available, which is carefully processed in our facility with precision traces of aluminum and magnesium, to produce a smoother etch. Our unique annealing and thermal flattening process helps shape grain growth to ensure the finished plate maintains a uniform, flat character. The zinc etches soft, yet is durable enough to stand the test of time. The result is superior zinc etching performance proven effective around the world.
There are different sizes available where as our default size is : 500mm x 1000mm, where as the thickness could range from 1mm – 7mm as per clientele request. With high grade PS coating on the plates and normal Polished plates, We Complete the process of giving services in etching plates and machines.
12 STEPS ZINC ETCHING PROCEDURE
1)- STORAGE:
Store zinc photoplates in a cool, dry place.
2)-ARTWORK:
Inspect negative carefully and opaque pinholes in the black areas. Pinholes result in pimply etching if not opaqued.
3)-EXPOSURE:
Expose using a Stouffer 21-Step Sensitivity Guide to a solid step 8-10. Overexposure causes excessive shadow-dot plugging and does not increase etching resistance of coating. Underexposure causes wash-off in development and etching failure.
4)-DEVELOPING:
Mix one part of Heated or Cold Hydro-Coat Developer with five parts water. Heated Hydro-Coat Developer should be used at 105°-115°F (41°-46°C). Cold Hydro-Coat Developer can be used at room temperature 70°-85°F (21°-29°C). In case of evaporation loss when using Hydro-Coat Developer, water alone should be added back to developer solution. DO NOT add back concentrate Hydro-Coat Developer to compensate for evaporation loss. Heated Hydro-Coat Developer should be changed when developing times exceed 90 seconds. Cold Hydro-Coat Developer used in trays should be changed daily.
5)-TOUCH UP:
Examine plate for flaws in the image areas retained on the plate and touch up as needed with Retouch Solution.
6)-WEIGH
Record initial plate weight on your etching log prior to etching. Scale must be capable of weighing to the nearest 1/4 ounce.
7)-DESCUM:
Descum Hydro-Coat zinc plates using a solution of sulfuric and nitric acid. Refer to descum formulas on next page. Wipe the descum solution across the plate both horizontally and vertically. For best results apply solution n°1 followed by solution n°2, with a final repeat application of solution n°1. Use separate descum pads for each solution. Rinse between solution applications.
8)-RINSE:
Rinse plates thoroughly with water after descumming.
9)-PLATE PROTECTOR:
An application of Express Guard Plate Protector is recommended prior to etching to enhance performance of etching bath by preventing oxidation which can cause pimples.
10)-ETCH:
Etch plates according to recommendations of etching machine manufacturers and additive technical data sheets.
11)-REPLENISH BATH:
Record plate weight after etching to determine proper acid replenishment. Refer to acid addition chart on last page. Use the following formula to calculate replenishment (where 1:1 represents 30 milliliters of acid per ounce of zinc dissolved into bath):
Initial plate weight – Post etching plate weight = amount of zinc dissolved
Rate of replenishment (1:1 or 1.5:1) will depend upon how much zinc is in the bath. Refer to recommendations of equipment manufacturer.
Example: 38.2 – 31.7 = 6.5 ozs. of zinc dissolved at a rate of 1:1 replenishment, 195 mls of acid are added to bath at a rate of 1.5:1 replenishment, 292,5 mls of acid are added to bath.
Check dip gauge and restore proper level in bath by adding water or draining excess.
12)-TOP REMOVAL (optional)
Use Hydro-Coat Top Remover II according to directions on label.
BASIC ZINC ETCHING BATH FORMULA:
- NITRIC ACID (42 Bé)……………….12%.
- SUPER ETCH or VELV-ETCH………………….3%.
- WATER………………………85%.
STANDARD ZINC ETCHING BATH SHOULD BE MAINTAINED AT 78° – 82°F (26° -28°C). IDEAL TEMPERATURE MAY VARY BASED ON APPLICATIONS.
ZINC DESCUM:
SOLUTION N°1: H2SO4 / HNO3
- 3.42 L WATER
- 350 ML CONCENTRATE SULFURIC ACID*
- 30 ML NITRIC ACID* (42 Bé)
(FORMULA MAKES 3.8 L OR 1 GAL. OF DESCUM SOLUTION).
SOLUTION N°2: HNO3
- 3.04 L WATER
- 760 ML NITRIC ACID* (42 Bé) 20% HNO3
(FORMULA MAKES 3.8 L OR 1 GAL. OF DESCUM SOLUTION).
* CAUTION: DO NOT ADD WATER TO ACID.
ALWAYS ADD ACID SLOWLY TO WATER TO AVOID A HAZARDOUS EXPLOSION.
RECOMMENDED BATH MAKEUP for SELECTED STANDARD INDUSTRY ETCHING MACHINES:
MACHINE | CAPACITY | ACID 42 Bé | SUPER ETCH or | STARTING
RPM |
||
VELV-ETCH | ||||||
ULTRAMATIC 40 | 40 LITERS | about | 5 LITERS | about | 1,5 LITERS | 500 – 550 |
ULTRAMATIC 90 | 90 LITERS | about | 10 LITERS | about | 3,0 LITERS | 500 – 550 |
ULTRAMATIC 200 | 200 LITERS | about | 25 LITERS | about | 6,0 LITERS | 500 – 550 |
BATH REPLENISHMENT VARIES SIGNIFICANTLY BY EQUIPMENT. REFER TO MANUFACTURER RECOMMENDATIONS. |
ACID ADDITION CHART
ZINC DISSOLVED | ACID ADDITIONS | ZINC DISSOLVED | ACID ADDITIONS | ||||
1 TO 1* | 1.5 TO 1* | 1 TO 1* | 1.5 TO 1* | ||||
OZS. | GRAMS | MLS | MLS | OZS. | GRAMS | MLS | MLS |
1 | 28 | 30 | 45 | 31 | 879 | 930 | 1395 |
2 | 57 | 60 | 90 | 32 | 907 | 960 | 1440 |
3 | 85 | 90 | 135 | 33 | 936 | 990 | 1485 |
4 | 113 | 120 | 180 | 34 | 964 | 1020 | 1530 |
5 | 142 | 150 | 225 | 35 | 992 | 1050 | 1575 |
6 | 170 | 180 | 270 | 36 | 1021 | 1080 | 1620 |
7 | 198 | 210 | 315 | 37 | 1049 | 1110 | 1665 |
8 | 227 | 240 | 360 | 38 | 1077 | 1140 | 1710 |
9 | 255 | 270 | 405 | 39 | 1106 | 1170 | 1755 |
10 | 284 | 300 | 450 | 40 | 1134 | 1200 | 1800 |
11 | 312 | 330 | 495 | 41 | 1162 | 1230 | 1845 |
12 | 340 | 360 | 540 | 42 | 1191 | 1260 | 1890 |
13 | 369 | 390 | 585 | 43 | 1219 | 1290 | 1935 |
14 | 397 | 420 | 630 | 44 | 1247 | 1320 | 1980 |
15 | 425 | 450 | 675 | 45 | 1276 | 1350 | 2025 |
16 | 454 | 480 | 720 | 46 | 1304 | 1380 | 2070 |
17 | 482 | 510 | 765 | 47 | 1332 | 1410 | 2115 |
18 | 510 | 540 | 810 | 48 | 1361 | 1440 | 2160 |
19 | 539 | 570 | 855 | 49 | 1389 | 1470 | 2205 |
20 | 567 | 600 | 900 | 50 | 1418 | 1500 | 2250 |
21 | 595 | 630 | 945 | 51 | 1446 | 1530 | 2295 |
22 | 624 | 660 | 990 | 52 | 1474 | 1560 | 2340 |
23 | 652 | 690 | 1035 | 53 | 1503 | 1590 | 2385 |
24 | 680 | 720 | 1080 | 54 | 1531 | 1630 | 2430 |
25 | 709 | 750 | 1125 | 55 | 1559 | 1650 | 2475 |
26 | 737 | 780 | 1170 | 56 | 1588 | 1680 | 2520 |
27 | 765 | 810 | 1215 | 57 | 1616 | 1710 | 2565 |
28 | 794 | 840 | 1260 | 58 | 1644 | 1740 | 2610 |
29 | 822 | 870 | 1305 | 59 | 1673 | 1770 | 2655 |
30 | 851 | 900 | 1350 | 60 | 1701 | 1800 | 2700 |
A photosensitive coating applied to a special Zinc photo engraving plate allows the user to chemically etch an image into the Zinc plate after exposing a film negative and developing that image on the plate. We also provide Polished , zinc and brass plates for chemical etching.
The most popular application for engraving plates is in creating dies to foil stamp and emboss a variety of printed products including greeting cards, folders, brochures, book covers and packaging materials. Other applications include thermal ‘kiss-cut’ dies, flexography, nameplates, decorative plaques, recognition awards and fabric/leather embossing. New applications are continually being developed.